Introduction
O2 Technologies have quickly become a driving force behind the advancements in Industry 4.0, particularly in the realm of manufacturing. With the rise of artificial intelligence (AI) systems and smart machines, O2 technologies have enabled businesses to achieve new levels of efficiency, productivity, and accuracy in their manufacturing processes. From predictive maintenance to intelligent quality control, O2 technologies are transforming the manufacturing landscape and paving the way for a smarter, more connected future. In this blog, we will explore the impressive impact of O2 technologies on Industry 4.0 and delve into the various ways AI is revolutionizing the manufacturing sector.
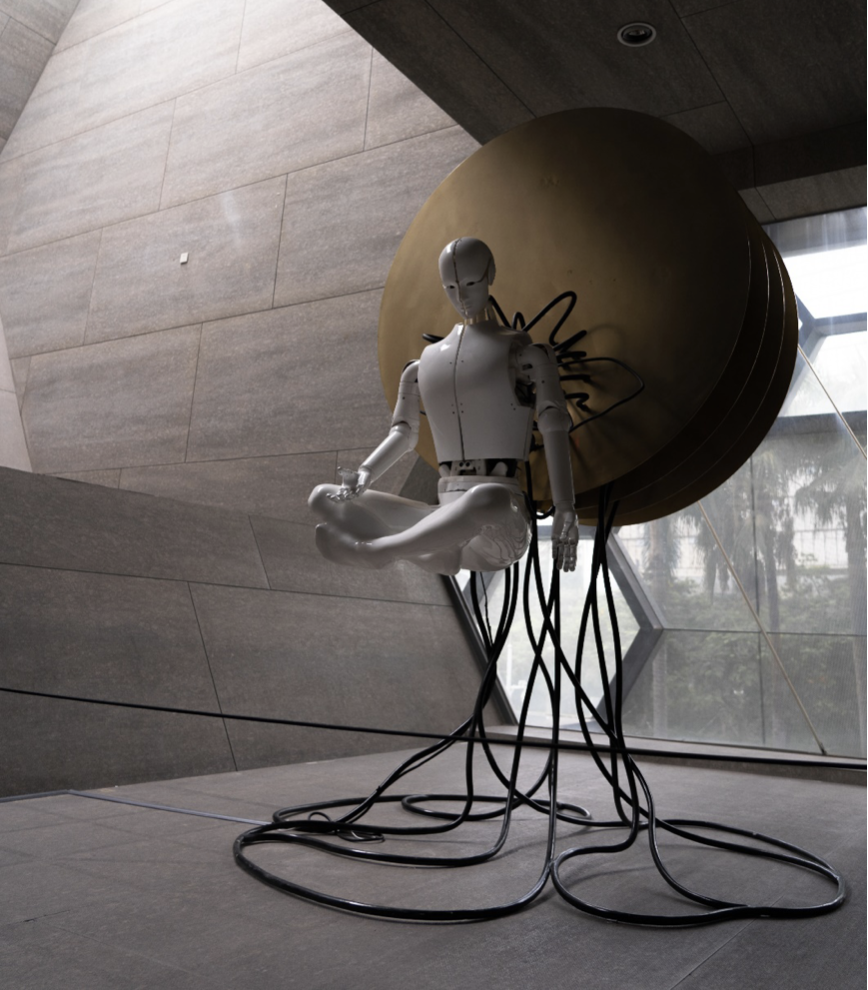
Understanding Industry 4.0 and its role in manufacturing
Before delving into the impact of O2 technologies on Industry 4.0, it is essential to have a clear understanding of what Industry 4.0 entails and its role in the manufacturing sector.
Industry 4.0, also known as the Fourth Industrial Revolution, encompasses the digital transformation of the manufacturing industry. It leverages advanced technologies such as artificial intelligence, the Internet of Things (IoT), cloud computing, and big data analytics to create smart factories and enable smarter, more efficient manufacturing processes.
One of the core principles of Industry 4.0 is the concept of connectivity. It emphasizes the integration of various components within the manufacturing ecosystem, including machines, sensors, production systems, and even supply chains. By connecting these components and enabling seamless communication, Industry 4.0 aims to create a highly optimized and agile manufacturing environment.
The adoption of Industry 4.0 technologies brings numerous advantages to the manufacturing sector. It enables real-time monitoring and control of production processes, allowing for immediate detection of issues and prompt resolution. This proactive approach helps minimize downtime, reduce waste, and improve overall production efficiency.
Furthermore, Industry 4.0 promotes the concept of intelligent automation. By combining AI and smart machines, manufacturers can automate repetitive tasks, optimize resource allocation, and enhance decision-making processes. This results in increased productivity, improved product quality, and reduced operational costs.
Additionally, Industry 4.0 facilitates the collection and analysis of vast amounts of data from various sources across the manufacturing value chain. This data can be leveraged to gain valuable insights into production processes, customer preferences, and market trends. With these insights, manufacturers can make data-driven decisions, identify areas for optimization, and even develop innovative products and services.
In summary, Industry 4.0 represents a significant shift in the manufacturing industry, driven by advanced technologies and the pursuit of efficiency and innovation. By embracing connectivity, intelligent automation, and data-driven decision-making, manufacturers can unlock new levels of productivity, profitability, and competitiveness.
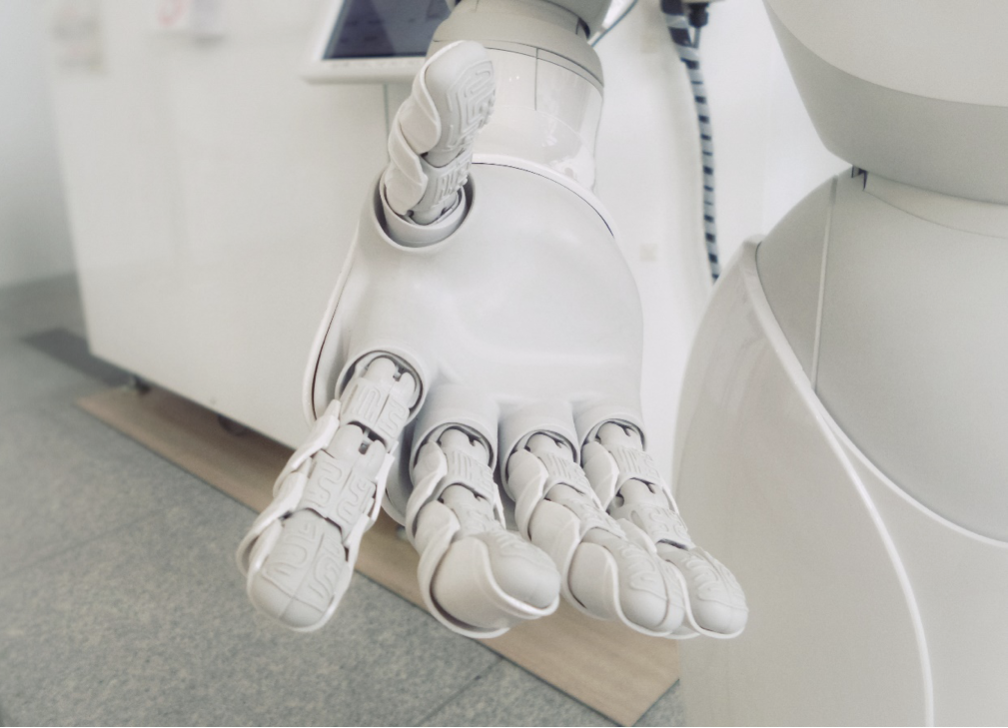
In the next section, we will explore the specific ways in which O2 technologies, in conjunction with AI, are revolutionizing the manufacturing landscape and furthering the goals of Industry 4.0.
The Rise of O2 Technologies
O2 technologies, are playing a crucial role in the revolution of Industry 4.0. These technologies leverage the power of artificial intelligence to enable smarter and more efficient manufacturing processes. With features like predictive maintenance, intelligent scheduling, and quality control, O2 technologies are transforming traditional manufacturing into a highly optimized and agile ecosystem.
One of the key benefits of O2 technologies is their ability to enable predictive maintenance. By analyzing data from sensors and machines in real time, AI-powered algorithms can detect potential equipment failures before they occur. This proactive approach allows manufacturers to schedule maintenance activities in advance, minimizing unplanned downtime and maximizing the overall equipment effectiveness.
Moreover, O2 technologies facilitate intelligent scheduling, ensuring efficient allocation of resources and optimal production planning. To create the best possible production schedules, AI algorithms can analyse a variety of variables, including machine availability, production capacity, and customer demand. This not only improves resource utilization but also helps manufacturers deliver products on time and meet customer expectations.
Quality control is another area where O2 technologies make a significant impact. Traditional quality control methods rely on manual inspections, which can be time-consuming and prone to human error. O2 technologies, on the other hand, enable automated quality control through the use of AI-powered vision systems and machine learning algorithms. These systems can quickly analyze product images or data streams, detecting defects or anomalies with high precision. By automating quality control, manufacturers can ensure consistent product quality and reduce the risk of faulty or defective products reaching the market.
Furthermore, O2 technologies enable real-time monitoring and data analysis, allowing manufacturers to gain valuable insights into their production processes. By collecting and analyzing data from various sources, including sensors, machines, and external systems, AI algorithms can identify patterns, trends, and correlations that may not be apparent to human operators. These insights can help manufacturers identify bottlenecks, optimize production workflows, and make data-driven decisions to improve overall operational efficiency.
The rise of O2 technologies is driving the transformation of the manufacturing industry, empowering manufacturers to achieve greater levels of productivity, profitability, and competitiveness. By adopting these technologies, manufacturers can harness the power of artificial intelligence to optimize production processes, improve resource allocation, and deliver high-quality products on time. In the next section, we will delve deeper into specific examples of O2 technologies and their applications in the manufacturing sector.
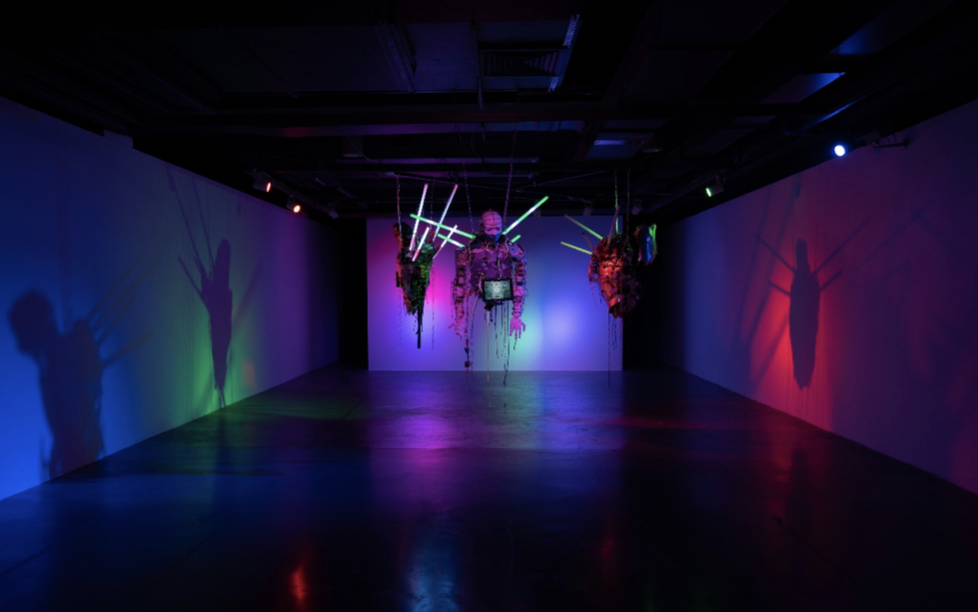
Harnessing the Power of AI in Manufacturing
Manufacturing is not an exception to how AI, or artificial intelligence, is revolutionising many other industries. By harnessing the power of AI, manufacturers can optimize production processes, improve resource allocation, and deliver high-quality products on time. In this section, we will delve deeper into specific examples of how AI is transforming the manufacturing sector.
Predictive maintenance is one of the most important uses of AI in manufacturing. By analyzing data from sensors and machines in real-time, AI-powered algorithms can detect potential equipment failures before they occur. This proactive approach allows manufacturers to schedule maintenance activities in advance, minimizing unplanned downtime and maximizing overall equipment effectiveness. With AI-enabled predictive maintenance, manufacturers can avoid costly breakdowns and ensure the continuous operation of their production lines.
Another area where AI is making a significant impact is in intelligent scheduling. To create optimised production schedules, AI algorithms can analyse a variety of variables, including machine availability, production capacity, and customer demand. This ensures efficient allocation of resources and helps manufacturers deliver products on time, meeting customer expectations. By using AI for intelligent scheduling, manufacturers can improve resource utilization and achieve optimal production planning.
Another crucial area of manufacturing that AI is transforming is quality control. Traditional quality control methods rely on manual inspections, which can be time-consuming and prone to human error. AI-powered vision systems and machine learning algorithms enable automated quality control, analyzing product images or data streams to detect defects or anomalies with high precision. By automating quality control processes, manufacturers can ensure consistent product quality and reduce the risk of faulty or defective products reaching the market.
Real-time monitoring and data analysis are also key benefits of AI in manufacturing. By collecting and analyzing data from various sources, including sensors, machines, and external systems, AI algorithms can identify patterns, trends, and correlations that may not be apparent to human operators. These insights can help manufacturers identify bottlenecks, optimize production workflows, and make data-driven decisions to improve overall operational efficiency. AI empowers manufacturers to gain valuable insights into their production processes, enabling continuous improvement and optimization.
In conclusion, AI is revolutionizing the manufacturing industry by harnessing the power of advanced algorithms and data analysis. With applications such as predictive maintenance, intelligent scheduling, automated quality control, and real-time monitoring, manufacturers can optimize production processes, improve resource allocation, and deliver high-quality products on time. By embracing AI, manufacturers can stay competitive in the ever-evolving landscape of Industry 4.0. In the next section, we will explore the challenges and future prospects of AI in manufacturing.
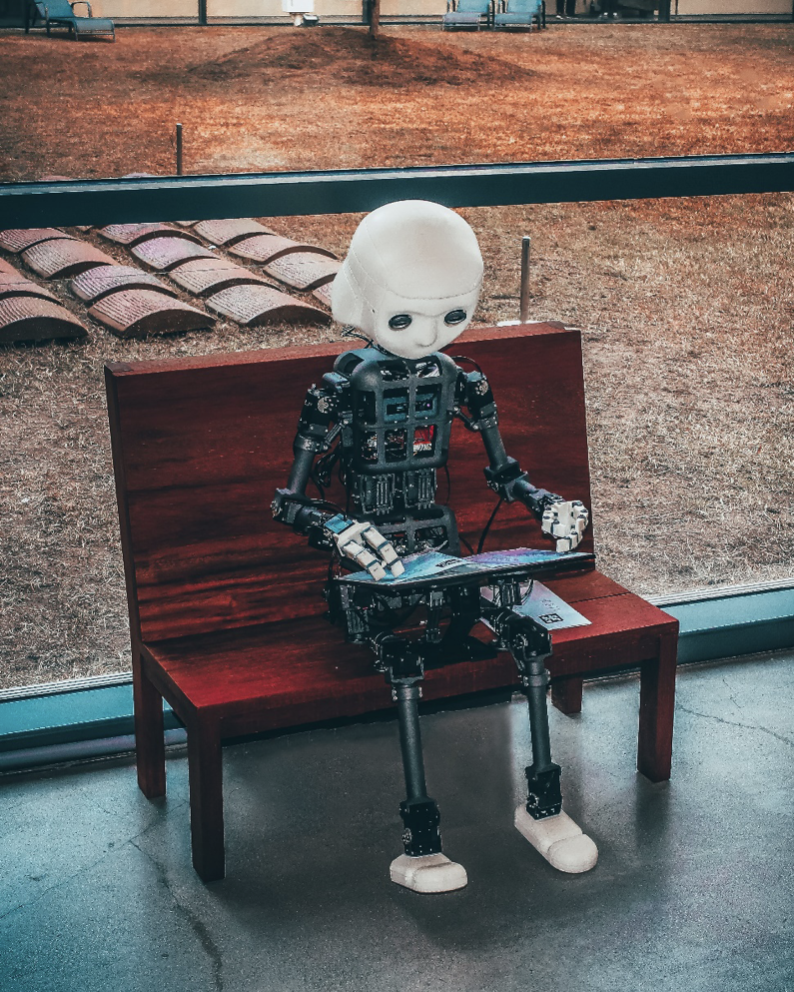
Transforming Manufacturing Processes with O2 Technologies
O2 Technologies, are playing a crucial role in revolutionizing the manufacturing industry, particularly in the context of Industry 4.0. These technologies leverage artificial intelligence (AI) and advanced algorithms to transform various manufacturing processes, leading to smarter and more efficient operations.
One of the key areas where O2 technologies are making an impressive impact is in predictive maintenance. By integrating AI algorithms with real-time data from sensors and machines, manufacturers can proactively identify potential equipment failures before they occur. This enables them to schedule maintenance activities in advance, minimizing unplanned downtime and optimizing overall equipment effectiveness. With the power of O2 technologies, manufacturers can significantly reduce operational costs and enhance productivity by avoiding costly breakdowns.
Another significant application of O2 technologies in manufacturing is in the realm of intelligent scheduling. By analyzing various factors such as machine availability, production capacity, and customer demand, AI-powered algorithms can generate optimized production schedules. This ensures efficient allocation of resources and enables manufacturers to meet customer expectations by delivering products on time. With O2 technologies, manufacturers can achieve optimal production planning and resource utilization, resulting in enhanced operational efficiency and customer satisfaction.
Quality control is another critical aspect of manufacturing that O2 technologies are transforming. Traditional quality control methods often rely on manual inspections, which can be time-consuming and subjective. However, by leveraging AI-powered vision systems and machine learning algorithms, manufacturers can automate the quality control process. These technologies can analyze product images or data streams in real-time to detect defects or anomalies with high precision. By implementing O2 technologies for automated quality control, manufacturers can ensure consistent product quality, minimize the risk of faulty products, and uphold their reputation in the market.
Real-time monitoring and data analysis are also key benefits offered by O2 technologies in the manufacturing industry. By collecting and analyzing data from various sources, including sensors, machines, and external systems, manufacturers can gain valuable insights into their production processes. AI algorithms can identify patterns, trends, and correlations that may not be apparent to human operators, enabling manufacturers to optimize production workflows and make data-driven decisions. With the power of O2 technologies, manufacturers can continuously improve their operational efficiency, identify bottlenecks, and implement targeted enhancements for overall process optimization.
In conclusion, O2 technologies are transforming manufacturing processes and empowering manufacturers to embrace the advancements of Industry 4.0. By leveraging the capabilities of AI and advanced algorithms, these technologies enable predictive maintenance, intelligent scheduling, automated quality control, and real-time monitoring. Manufacturers can optimize their operations, improve resource allocation, and deliver high-quality products on time, ultimately staying competitive in the ever-evolving landscape of the manufacturing industry. As we look towards the future, O2 technologies hold immense potential to further revolutionize manufacturing processes and drive unprecedented levels of efficiency and innovation.
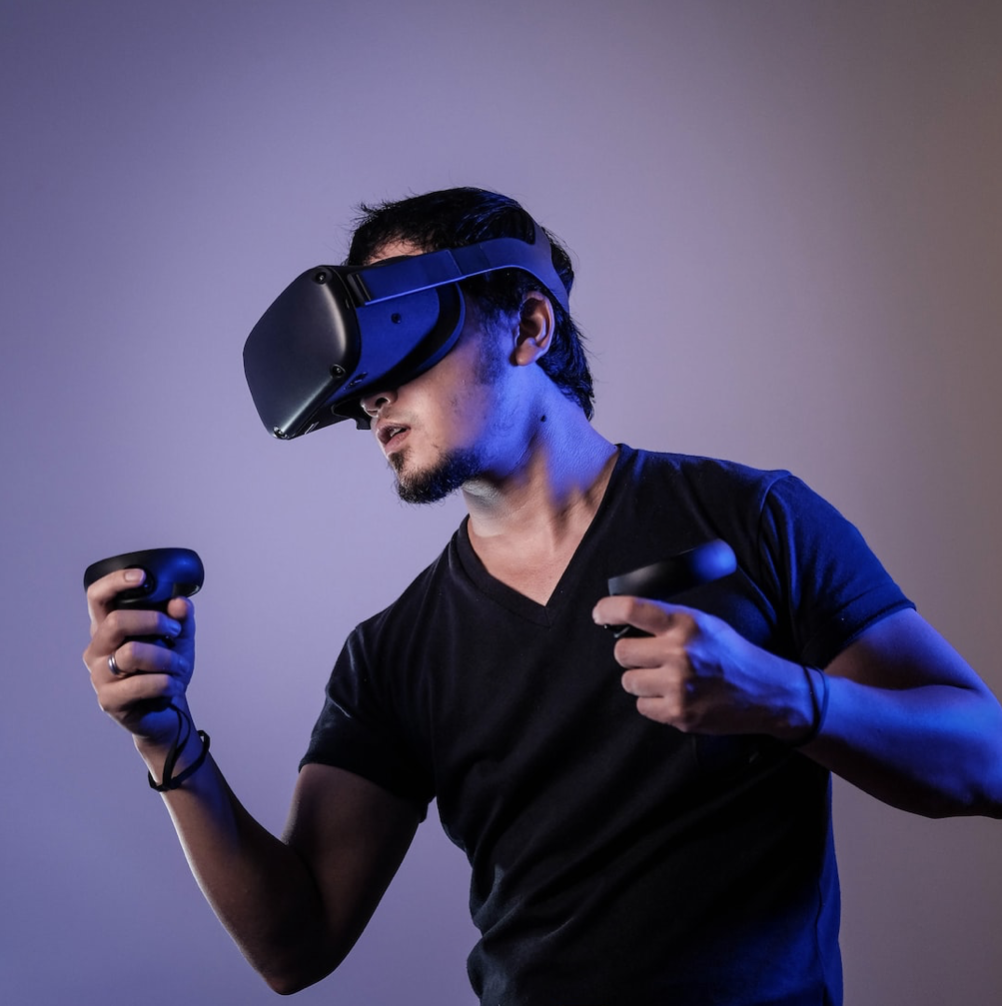
One of the most significant advantages that O2 technologies bring to the manufacturing industry is the ability to achieve unparalleled levels of efficiency and accuracy through the integration of AI-powered solutions. These technologies leverage artificial intelligence algorithms to streamline various processes, optimize resource allocation, and enhance overall operational performance.
One area where AI-powered solutions have a remarkable impact is in predictive maintenance. By analyzing real-time data from sensors and machines, these solutions can proactively identify potential equipment failures before they occur. This enables manufacturers to schedule maintenance activities in advance, avoiding costly breakdowns and minimizing unplanned downtime. By implementing AI-powered predictive maintenance, manufacturers can optimize their maintenance processes, reduce operational costs, and ensure the seamless functioning of their production lines.
Another significant application of AI-powered solutions in the manufacturing industry is in the realm of intelligent scheduling. By considering various factors such as production capacity, machine availability, and customer demand, these solutions can generate optimized production schedules. This ensures efficient allocation of resources and enables manufacturers to meet customer expectations by delivering products on time. With AI-powered intelligent scheduling, manufacturers can achieve optimal production planning, minimize idle time, and maximize resource utilization.
Accuracy is also a key benefit offered by AI-powered solutions in manufacturing. Traditional quality control methods often rely on manual inspections, which can be time-consuming and subjective. However, by leveraging AI-powered vision systems and machine learning algorithms, manufacturers can automate the quality control process. These technologies can analyze product images or data streams in real-time to detect defects or anomalies with high precision. By implementing AI-powered quality control solutions, manufacturers can ensure consistent product quality, minimize the risk of faulty products, and uphold their reputation in the market.
Furthermore, AI-powered solutions enable real-time monitoring and data analysis, providing valuable insights into production processes. By collecting and analyzing data from various sources, including sensors, machines, and external systems, manufacturers can identify patterns, trends, and correlations that may not be apparent to human operators. This allows them to optimize production workflows, identify bottlenecks, and make data-driven decisions for process optimization. With AI-powered real-time monitoring and data analysis, manufacturers can continuously improve their operational efficiency and drive continuous improvement initiatives.
In conclusion, the integration of AI-powered solutions enabled by O2 technologies is revolutionizing the manufacturing industry by enabling unprecedented levels of efficiency and accuracy. These solutions facilitate predictive maintenance, intelligent scheduling, automated quality control, and real-time monitoring, enabling manufacturers to optimize their operations, improve resource allocation, and deliver high-quality products on time. As we look towards the future, AI-powered solutions hold immense potential to further enhance manufacturing processes, drive innovation, and propel the industry towards a highly efficient and competitive future.
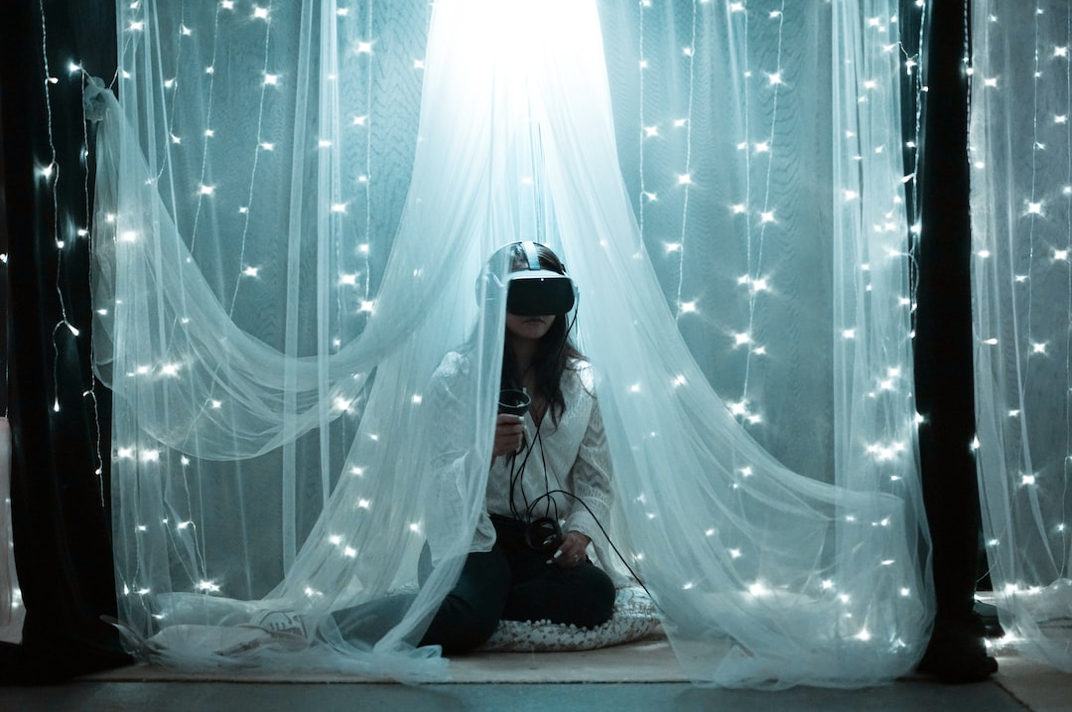
Enhancing Workforce Safety with O2 Technologies
In addition to achieving efficiency and accuracy, O2 technologies powered by artificial intelligence have a significant impact on enhancing workforce safety in the manufacturing industry. These technologies leverage advanced sensing capabilities, real-time data analysis, and machine learning algorithms to create a safer work environment for employees.
One crucial application of O2 technologies in enhancing workforce safety is the implementation of AI-powered predictive maintenance. By continuously monitoring equipment and analyzing real-time data from sensors, these technologies can detect anomalies or potential failures before they occur. This proactive approach allows manufacturers to schedule maintenance activities in advance, minimizing the risk of unexpected equipment breakdowns that can pose safety hazards to workers. By ensuring that machinery is in optimal working condition, manufacturers can create a safer environment for their employees.
Furthermore, O2 technologies enable the implementation of AI-powered safety monitoring systems. These systems utilize sensors and AI algorithms to detect potential safety hazards, such as unauthorized access to restricted areas or the presence of hazardous substances. By constantly monitoring the production floor, these technologies can alert operators and supervisors in real-time, allowing them to take immediate action to mitigate risks and ensure the safety of the workforce. AI-powered safety monitoring systems not only enhance workplace safety but also contribute to the prevention of accidents and injuries.
Another significant application of O2 technologies in enhancing workforce safety is the use of AI-powered robotics and automation. These technologies can automate repetitive and dangerous tasks, reducing the need for human intervention in potentially hazardous situations. By deploying robots equipped with advanced sensors and intelligent algorithms, manufacturers can ensure that workers are not exposed to dangerous environments or heavy machinery. This reduces the risk of accidents and injuries, creating a safer working environment for the workforce.
Additionally, O2 technologies enable the integration of wearable devices and smart personal protective equipment (PPE). These devices, equipped with sensors and AI capabilities, can monitor vital signs, detect hazardous conditions, and provide real-time feedback to workers. For example, smart helmets can detect elevated levels of gas or heat, alerting workers to potential dangers and prompting them to take appropriate action. Wearable devices and smart PPE enhance the safety of workers by providing them with valuable information and warnings in real-time.
In conclusion, O2 technologies powered by artificial intelligence have a significant impact on enhancing workforce safety in the manufacturing industry. Through AI-powered predictive maintenance, safety monitoring systems, robotics and automation, and wearable devices, manufacturers can create a safer work environment, reduce accidents and injuries, and protect their most valuable asset—their employees. As the use of O2 technologies continues to evolve and advance, the potential for further enhancing workforce safety in the manufacturing industry is immense.
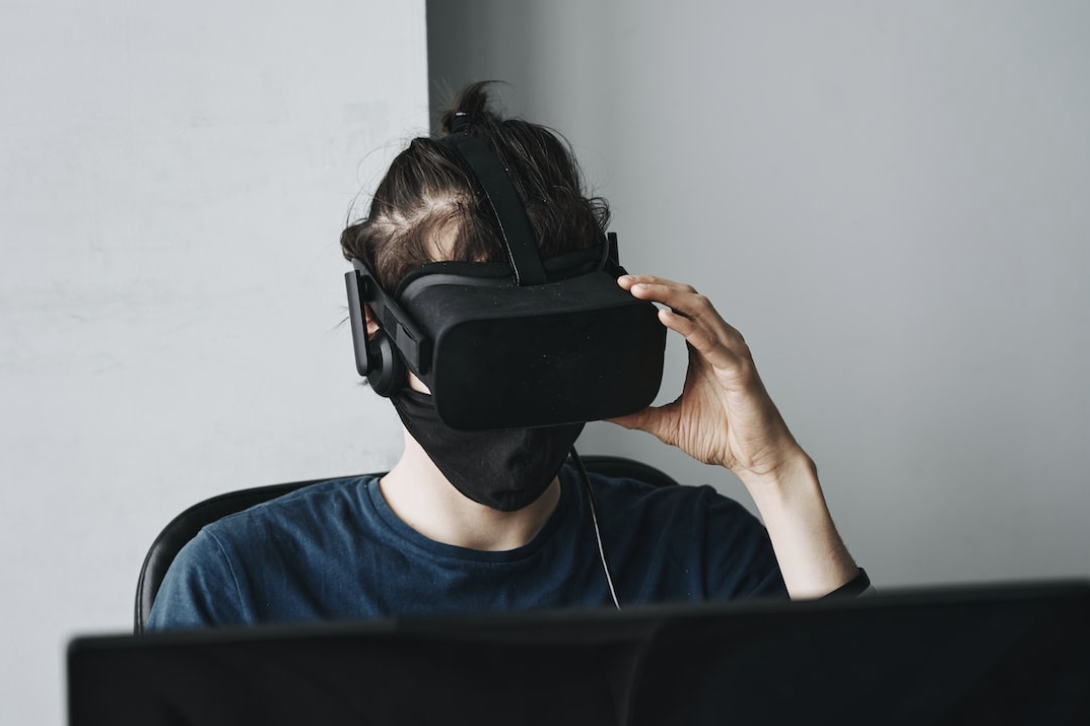
The Future of Manufacturing with O2 TechnologiesÂ
As O2 technologies powered by artificial intelligence continue to advance and evolve, the future of manufacturing is set to witness significant transformations. These technologies are revolutionizing the industry by improving efficiency, accuracy, and now, safety. Here are some key advancements and trends that are expected to shape the future of manufacturing with O2 technologies:
1. Increased Automation and Robotics: The integration of AI-powered robotics and automation will further enhance the manufacturing process. With advanced sensors, intelligent algorithms, and machine learning capabilities, robots will be able to perform complex tasks with precision and accuracy. This will not only increase productivity but also minimize the risk of accidents and injuries by reducing human intervention in hazardous situations.
2. Enhanced Predictive Maintenance: The implementation of AI-powered predictive maintenance systems will become even more sophisticated in the future. By leveraging real-time data analysis and machine learning algorithms, manufacturers will be able to detect potential equipment failures before they occur. This will enable proactive maintenance measures and minimize the risk of unexpected breakdowns, ensuring a safer working environment for employees.
3. AI-powered Safety Monitoring Systems: The future of manufacturing will witness the widespread adoption of AI-powered safety monitoring systems. These systems will utilize sensors, AI algorithms, and real-time data analysis to detect potential safety hazards in the production floor. By alerting operators and supervisors in real-time, these technologies will enable immediate action to mitigate risks and ensure the safety of the workforce.
4. Advancements in Wearable Devices and Smart PPE: Wearable devices and smart personal protective equipment (PPE) will become increasingly sophisticated and intelligent. Equipped with sensors and AI capabilities, these devices will monitor vital signs, detect hazardous conditions, and provide real-time feedback to workers. This will enhance the safety of employees by alerting them to potential dangers and enabling them to take appropriate action promptly.
5. Collaborative Robotics: The future of manufacturing will witness the rise of collaborative robots, also known as cobots. These robots will be capable of working alongside human workers, assisting them in complex tasks and ensuring their safety. Through advanced sensors and AI algorithms, cobots will have the ability to detect the presence of humans and adjust their movements accordingly, minimizing the risk of accidents and injuries.
6. Integration of Virtual and Augmented Reality: Virtual and augmented reality technologies will play a significant role in the future of manufacturing. These technologies will provide immersive training experiences for workers, enabling them to learn complex tasks in a safe virtual environment. Additionally, augmented reality can be used to provide real-time instructions, overlaying digital information onto the physical workspace, further enhancing safety and accuracy.
The future of manufacturing with O2 technologies is poised to be safer, more efficient, and highly automated. By embracing these advancements, manufacturers can not only enhance their productivity and profitability but also prioritize the safety and well-being of their workforce. As the capabilities of O2 technologies continue to advance, the potential for further innovation and improvement in the manufacturing industry is vast. The future is bright for manufacturers who embrace the power of O2 technologies.